Principle of operation
Burning high sulfur coal (over 2% of sulfur content) creates sufficient amount of SO3 in flue gases to achieve optimum ash resistivity. As nowadays most of boilers burn low sulfur coal, the aim of conditioning process is to inject “missing” quantity of SO3 into the flue gas stream at ESP inlet. Presence of sulfur trioxide in fumes influences ash properties; reduces its resistivity, increases cohesiveness and to certain degree change particle size. All these modifications are important from precipitation effectiveness point of view, however dust resistivity has greatest potential to be used. Figure 1 shows how dust resistivity depends on SO3 content and temperature of flue gas. Even small quantity (few ppm) of SO3 added to flue gas stream causes significant drop of ash resistivity particularly in temperature range typical for flue gas temperature on ESP inlet.
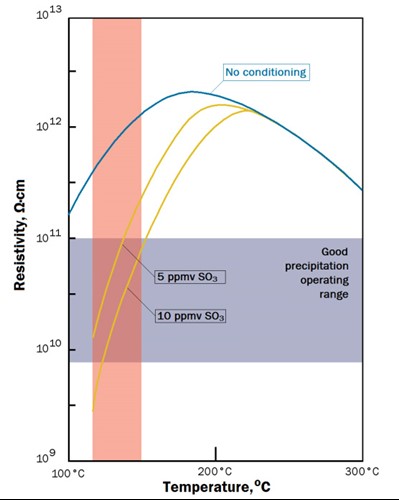
Fig. 1. Ash resistivity versus SO3 content and gas temperature
It is commonly regarded that the resistivity 1010 to 1011 Ω·cm is an optimal range. When ash resistivity is below this range (blue strip in the figure 1), the charged particles too easily release the charge which in consequence cause excessive entrainment of the collected ash. On the other hand, fly ash with resistivity over 1011 Ω·cm exhibit opposite phenomena: dust is held on the collecting plates very tight leading to back corona which reduces ESP collecting efficiency.
Sulfur trioxide naturally combines with the moisture in the flue gas to create mist of sulfuric acid. Then, sulfuric acid immediately reacts with the fly ash particles to form a thin conductive film, which eventually lowers the fly ash resistivity. Therefore, the main aim of FGC is to keep the fly ash resistivity in a good precipitation range, allowing constantly low emission with a broad range of coal types. Required concentration of SO3 in flue gas depends on many factors but usually does not exceed 10 to 15 ppm.
Figure 2 shows an example of how ESP efficiency depends on two factors: dust resistivity and specific collection area (SCA) of ESP.
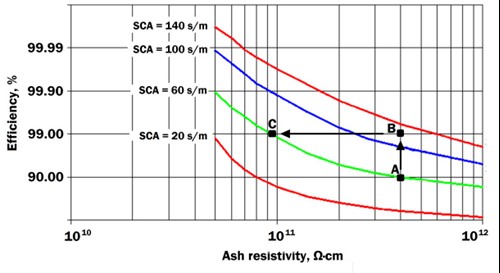
Fig. 2. ESP efficiency vs. dust resistivity and SCA
Assuming that the target is to improve poor efficiency of existing ESP of low SCA (point A on green curve) there are two alternative solutions (not neglecting upgrade steps like e.g. CFD or SPC): either to increase size of ESP (see point B) or to reduce dust resistivity via flue gas conditioning (point C on green curve).
Modern FGC system
A layout of modern Pentol’s FGC installation is shown in the figure 3.
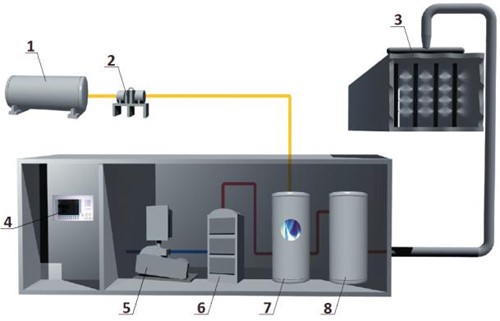
Fig. 3. FGC plant layout [2];
(1) sulfur tank, (2) pumps, (3) flue gas duct,
(4) converter unit, (5) air blower, (6) air heater,
(7) sulfur burner, (8) catalytic converter
Depending on the availability of liquid or granulated sulfur, an appropriate sulfur storage tank (1) is chosen. The tank is heated up to approx. 130°C (process steam is usually used as heating medium) in order to reduce sulfur density. Also the sulfur transportation pipeline from the tank to the burner must be heated. The metering pump (2) transports liquid sulfur from the tank to the burner (7). Combustion air to the burner is first preheated by means of electrical heaters (6) and then delivered (by fan(5)) to the burner. Heating the air stream well above the self-ignition temperature of sulfur assures that there is no need of using additional sulfur ignition system. Next, SO2 from the burner is converted to SO3 by means of the catalyzer (8). The last stage of the process is injection of SO3/air mixture to the flue gas duct via injection probes (3).
Nowadays, FGC installations work automatically (following the boiler load) and are controlled via remote access. Therefore they require minimum attention from the Operator staff - in practice maintenance works are limited to periodic check-ups and refilling of the sulfur tank.
Pictures of FGC installation
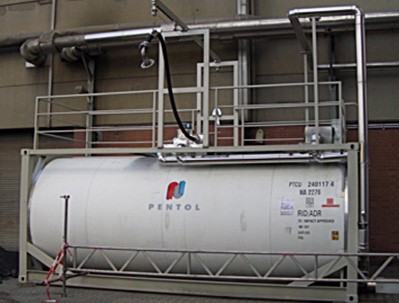
Fig. 4. Sulfur storage tank

Fig. 5. Inside of FGC container (on the left: sulfur burner, air heaters in the background, on the right: air blower)
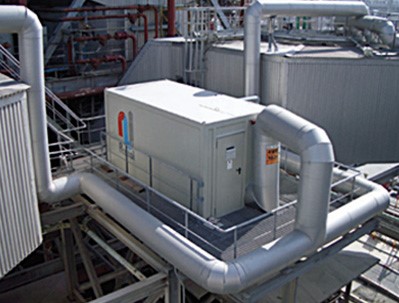
Fig. 6. FGC unit with piping, and probes for SO3 injection
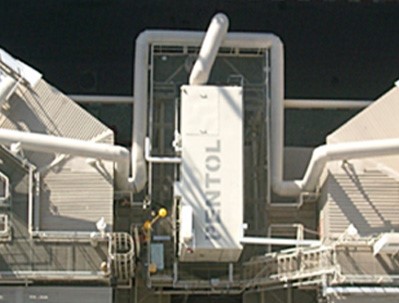
Fig. 7. FGC unit with piping, and probes for SO3 injection (view from top)
ESP condition before FGC trial
General rule says that optimum performance of FGC is achieved when ESP mechanical and electrical conditions are good, however there are examples proving that even in case of extremely poor ESP conditions FGC may result in significant reduction in dust emissions.
Thorough check of ESP condition is necessary to determine feasibility of FGC and to agree with the plant operator necessary scope of works to be done to achieve its optimum performance. One of the most efficient diagnostic tools are current/voltage characteristics.
Applications
Generally, the main application of flue gas conditioning is in combination with:
- coal boilers in Power Plants,
- coal boilers in CHPs,
- CHP boilers in Steelworks (where fuels is usually mixture of blast furnace gas and coke gas),
- sintering strands in ore sintering plants.
Nowadays, more and more often FGCs are used in combination with wet FGD. Flue gas desulfurization plants downstream of the ESP receive less fly ash. With reduced dust load arriving in the FGD, the gypsum can grow to a larger size containing less moisture. In addition the color of gypsum is much whiter. These are critical parameters determining gypsum quality and its price. In countries like Germany or France majority of conditioning installations are recently installed to protect wet FGD plants.
Measuring of SO3
Pentol is a producer of one of essential devices for monitoring the operation of the FGC units: an analyzer for SO3 (in portable and stationary version). It is used to determine SO3 concentration on the inlet to ESP as well as to make sure/indicate that only traces of sulfur trioxide appear in flue gas after ESP. Read more about SO3 analyser - here.
|
1991 kB |
Flue Fas Conditioning - Reduce Solid Emission |
|
373 kB |
Flue Fas Conditioning - Optimisation of Dust Collection in the Coal Fired Power Station of Herne, Germany |
|
5844 kB |
SO3 monitor - How much SO3 do you generate? |
|
1729 kB |
SO3 monitor - Continuous measurement of sulphuric acid vapour in combustion gases using a portable automatic monitor |
|
509 kB |
Flue gas conditioning system (ICESP 2016) |